MARITIME, AEROSPACE AND OIL AND GAS INDUSTRY: USES OF MONEL 400
- November 10, 2023
- Posted by: vAchESpAVe388ema5hetray8
- Category: BSW blog EN
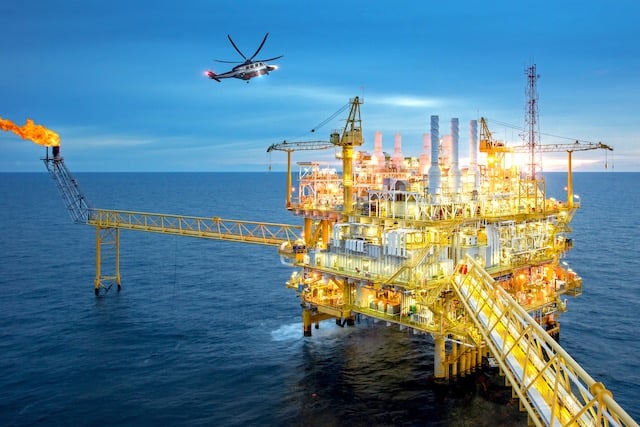
Monel 400 is a fairly simple alloy that can stand up to the most demanding conditions. With a minimum of 63% nickel and 28-34% copper, it was created over a century ago to be a cheaper substitute for pure nickel while retaining all the metal’s key properties. It’s fair to say that Monel 400 has met – and exceeded – this brief.
In addition to the main nickel and copper components, Monel 400 also contains small amounts of iron for reinforced strength (max 2.5%), manganese for enhanced corrosion resistance and thermal conductivity (max 2%), and trace amounts of silicon, carbon and sulphur.
As you would expect from a nickel alloy, Monel 400 is very versatile and has a great range of properties. But two characteristics really make it stand out among its peers. Firstly, it combines high strength with exceptional resistance to corrosion by both alkaline and acidic media. And secondly, it retains these characteristics at a vast range of temperatures, including extreme cold.
Let’s have a look at the chief fields of application for Monel 400: the maritime, oil & gas, and aerospace industries.
MARITIME USES OF MONEL 400
Monel 400’s resistance to cryogenic temperatures, together with its resistance to seawater corrosion, make it an exceptional choice for critical applications in the maritime context. In terms of practicality, economy and safety, it is simply unbeatable.
In shipbuilding, piping for crucial elements such as water curtain systems, firefighting systems, cooling water systems and daily seawater systems was traditionally made from copper alloys. In addition to being relatively expensive, these materials would inevitably fall prey to corrosion over time. The combination of constantly flowing seawater and the sulphides present in the water lead to pitting corrosion, which in turn leads to leaky pipes. And these can do significant damage even before they are detected.
Not only is Monel 400 a more economical option for this kind of piping, it also has a much longer operative life when exposed to seawater. The key to this is its high corrosion resistance, which – unlike standard copper alloys – is not significantly affected by the flow of seawater. .
As a rule, the faster the seawater flows over a metal component, the higher the degree of corrosion. Monel alloys are the only copper-containing alloys that can resist this accelerating effect, maintaining a low and steady corrosion rate of a maximum of 0.03mm per year. This means that pipes made with Monel 400 can go for much longer without having to be replaced, and the small degree of corrosion that they do undergo follows a regular and predictable pattern. Maintenance is easy to plan, and there’s no need to worry about sudden, cataclysmic failure when the ship is actually at sea. .
As well as piping, in the shipbuilding industry you’ll find Monel 400 used for propellers and heat exchangers, valve stems and pump shafts, freshwater and gasoline tanks, nuclear engineering components, and more. .
OIL AND GAS APPLICATIONS OF MONEL 400.
This combination of affordability, high strength, temperature resistance and corrosion resistance makes Monel 400 suitable for many critical applications in extreme conditions. Another key area is the oil and gas industry, where components are routinely exposed to extreme heat and corrosive media.
Monel 400 has proved as revolutionary in oil and gas production as it has in shipbuilding. Only a few years ago, expensive and dangerous component failure was still a common feature of both onshore and offshore extraction. Even the most corrosion-resistant alloys available at that time would still succumb eventually when exposed to extremely corrosive chemicals such as hydrofluoric acid – a major risk to health and safety.
Monel 400 is durable and resistant even when exposed to the harshest acids, but it’s just as resistant to corrosion by an alkaline medium like seawater. This makes it a particular asset to offshore oil and gas production, and you’ll find it used at every stage of the process, from extraction to refining. Tooling, extraction equipment and wellheads are all common applications for this super-tough alloy.
AEROSPACE APPLICATION OF MONEL 400
Cost-effective and high-performing, Monel 400 has been a stalwart choice for aerospace engineers since the 1960s. One of its first applications was a truly cutting-edge one, making frames and skins for rocket aeroplanes. But that’s just the beginning when it comes to the many ways this alloy can be put to use.
The aerospace industry has its own set of challenges. Not only do components need to be resistant to corrosion – for example, from fuels and exhaust gases – but they also need to be strong, light, and able to retain their integrity and properties under extreme pressure.
Because Monel 400 displays great resistance to stress-cracking as well as corrosion, you’ll find it used in many crucial applications. These include landing gear components, combustion chambers, safety wiring, and rivets in the exhaust and engine systems.
As with other applications, Monel 400 and other Monel alloys are a reliable choice in more ways than one. Not only is the material itself comparatively affordable to start with, but its strength and resistance make it an even more economical choice.
AFFORDABLE, BUT NOT CHEAP
Of course, economy can often mean cutting corners, but that isn’t the case here. The long operative life of Monel 400, even under severe stress and in extreme conditions, is certainly a money-saver, since components need to be replaced much less often. But above all, it’s a crucial safety feature.
Whether in shipbuilding, oil and gas production or aerospace, a corroded pipe or broken valve can endanger lives. That’s why the Monel alloy range is such an asset from a health and safety perspective, too.
We sell Monel 400 pipes, tubes, pipe fittings and flanges. We also supply its sibling alloy Monel K-500, which is precipitation-strengthened. If you’re interested in making a purchase or finding out more about these tough, versatile and resistant alloys and their applications, just contact us